Systèmes de fondation de pompe : une tendance croissante
Une tendance croissante dans les nouvelles installations de pompes, la réparation et le remplacement est l'utilisation d'un système de fondation monobloc. De tels systèmes intègrent la surface de montage d'équipement habituelle (plaque de base) ainsi que la colonne de support en béton (piédestal ou tampon d'entretien ménager) dans une unité homogène. Ces systèmes permettent d'économiser un temps et des dépenses considérables en arrivant sur site dans un seul emballage, fournissant une structure entièrement résistante à la corrosion qui accélère l'installation en éliminant de nombreuses étapes du processus. Les installations typiques vont du début à la fin en moins de deux jours. Le résultat final est une solution à moindre coût de possession qui fournit un environnement fiable pour les pompes et les équipements rotatifs.
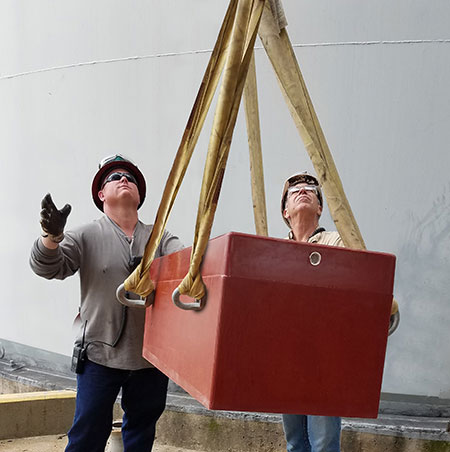
Installation
Dans la plupart des installations, un socle en béton est formé et construit prêt à accepter une plaque de base d'équipement séparée. Ces piédestaux, ou tampons d'entretien ménager, sont conçus pour surélever l'équipement et aider à maintenir les lignes centrales de la tuyauterie. Les systèmes complets de fondation en composite polymère arrivent en une seule pièce, prêts à être installés et éliminent le besoin d'une armature en béton et de longs cycles de durcissement pouvant durer plusieurs semaines.
Récemment, une grande usine d'éthanol a remplacé une plaque de base métallique défaillante par un nouveau système de fondation en moins d'une journée. En utilisant un coulis à durcissement rapide, l'usine a pu enlever l'ancienne base et la dalle de béton partielle, installer un nouveau système de fondation et monter une pompe et un moteur de 150 chevaux (hp) dans un délai de moins de 10 heures à partir de indemnite.
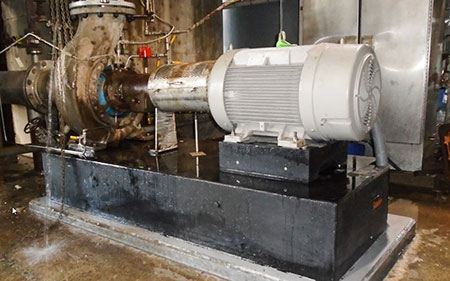
Caractéristiques supplémentaires
Environnement résistant à la corrosion
Les systèmes de fondation intégrés de base et de piédestal offrent un environnement résistant à la corrosion. Le remplacement du métal et du béton sujets à la corrosion élimine le besoin d'installer et d'entretenir des revêtements coûteux et protège le lien critique entre la base de l'équipement et la surface de montage surélevée. De plus, l'élimination du besoin de boulons d'ancrage exposés élimine les sources potentielles de contamination et de corrosion, ajoutant de la vie à la structure.
Les surfaces de montage de précision plates sont généralement inférieures à 0,002 pouce par pied d'alignement final de l'équipement, tandis que la résistance à la compression élevée des matériaux composites polymères peut être quatre à cinq fois supérieure à celle du béton typique. Les conceptions incorporant des renforts structurels ainsi que des options de construction solides empêchent la fissuration et éliminent le besoin de remplissage sur le terrain. La construction de ces systèmes monoblocs dans un environnement contrôlé peut permettre de fournir une structure correctement construite et durcie. Les composites polymères offrent un amortissement des vibrations tout en maintenant le rapport recommandé de trois à cinq fois entre l'équipement et le poids de la fondation.
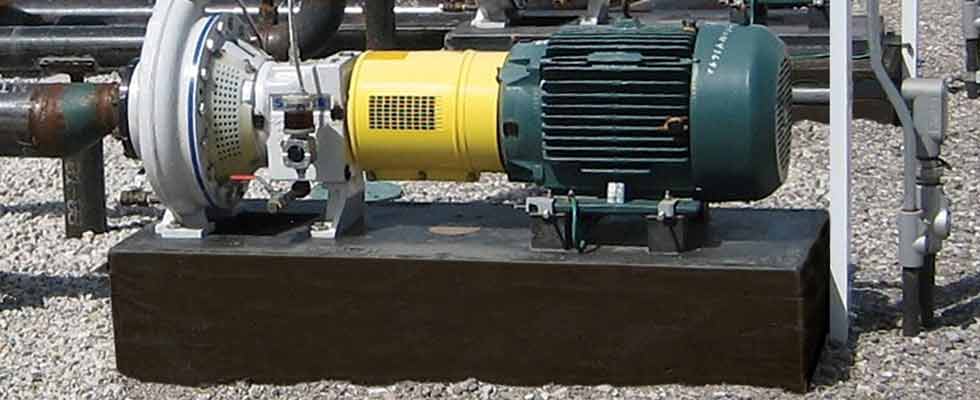
Emplacements de montage durables et flexibles
Des inserts filetés et des plaques de montage métalliques de plusieurs options de matériaux peuvent être intégrés pendant le processus de coulée pour fournir des emplacements de montage sûrs et stables pour l'équipement. Les emplacements de montage renforcés et robustes dépasseront généralement la résistance nominale du matériel utilisé pour sécuriser l'équipement. L'ajout ou la réparation d'emplacements d'inserts filetés pour monter des équipements supplémentaires ou des changements d'équipement peuvent être effectués manuellement sur le terrain pour la plupart des applications.
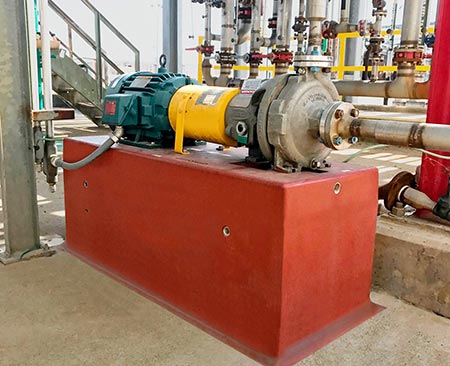
Modalités d'installation
Les systèmes de fondation peuvent être installés selon plusieurs dispositions. Ils sont souvent montés en surface avec du coulis, enterrés dans un environnement souterrain ou mis en place de manière autonome. Des conceptions flexibles peuvent être adaptées à de nombreuses applications différentes en fonction des besoins spécifiques de l'équipement, de l'environnement existant et des paramètres de fonctionnement.
Montage en surface
Le plus souvent, ces systèmes sont ancrés et cimentés sur une surface sécurisée existante (Image 2). En règle générale, la fondation préfabriquée arrivera sur le chantier configurée à ou près de la hauteur de conception. Une fois que le système est nivelé et maintenu mécaniquement en place, une petite quantité de matériau de coulis époxy est utilisée pour lier et sceller le fond de la coulée de fondation à la surface existante. Une fois durcies, les formes de coulis peuvent être facilement retirées en conjonction avec l'équipement de montage et d'alignement. Ces activités se produisent généralement en environ un à deux jours.
Certaines conceptions peuvent être partiellement enfouies sous le niveau du sol et entourées de gravier, de terre ou de ciment standard (image 3). L'installation typique consiste en une cavité creusée dans un sol ferme compacté, puis en nivelant le système de fondation contre une petite disposition solide telle qu'un bloc. Un matériau de remblai ou un béton à prise rapide est suffisant pour maintenir fermement l'unité. Les fondations correctement renforcées ne peuvent pas se plier, se tordre ou se diaphragmer, de sorte que la surface de montage
restera à plat, gardant l'équipement rotatif dans l'alignement. Une conception de construction solide peut fournir les rapports de poids fondation/équipement adéquats pour la plupart des applications. Le montage souterrain offre une solution de fondation rapide et sûre pour les équipements montés à l'intérieur et à l'extérieur.
Environnements autonomes
Les systèmes de fondation peuvent également être utilisés dans un environnement autonome pour une utilisation temporaire ou sur une surface non perméable telle qu'une digue revêtue de caoutchouc ou une zone de confinement spécialisée (Image 4). Les structures peuvent être placées sur n'importe quelle surface plane relativement solide et être autorisées à se déplacer légèrement avec les forces et les mouvements de la tuyauterie. La masse globale de la structure fournira, dans la plupart des applications, un amortissement adéquat des vibrations et une surface de montage rigide pour maintenir l'équipement correctement aligné. Un matériau de plinthe époxy ou un gel d'ancrage peut empêcher le liquide de s'accumuler sous la fondation. Dans la plupart des cas, le fluide de fond ne causera pas de problème en raison de la conception entièrement résistante à la corrosion de la structure.
Avantages de coût
En plus des avantages financiers des temps d'installation raccourcis, le coût d'achat peut être inférieur. La main-d'œuvre pour construire et installer les coffrages, couler le béton, enlever et sceller/finir les surfaces peut être coûteuse pour compléter le piédestal surélevé. Ces socles nécessitent également la fixation d'une plaque de base d'équipement pour terminer l'installation et être prêts pour l'équipement.
Dans de nombreux cas, des bases métalliques renforcées avec des surfaces usinées coûteuses sont spécifiées pour obtenir rigidité et planéité. Ces bases métalliques sont généralement des mises à niveau à partir de conceptions standard et peuvent ajouter des coûts à l'achat. Ces bases doivent subir une préparation de surface puis être montées, nivelées et coulées sur le socle en béton. Souvent, une quantité considérable de coulis époxy est nécessaire pour remplir les sections creuses de la plaque de base.
Une base en composite polymère intégrée au système de fondation peut éliminer la nécessité de plusieurs de ces étapes et coûts tout en offrant les mêmes avantages fiables dans une conception résistante à la corrosion.
Les systèmes de fondation intégrale monobloc offrent une solution fiable et peuvent fournir un faible coût de possession. Ils sont généralement construits pour une application spécifique et peuvent être installés dans de nombreuses configurations, formes et tailles de montage différentes. La construction en composite polymère offre une longue durée de vie dans les environnements corrosifs et élimine le besoin de revêtements supplémentaires et d'entretien périodique. Les caractéristiques d'amortissement des vibrations peuvent assurer une longue durée de vie aux équipements rotatifs, ce qui se traduit par une fiabilité accrue.